Toolboxmeeting: van definitie naar uitvoering
Alle factoren voor een succesvolle meeting op een rij.
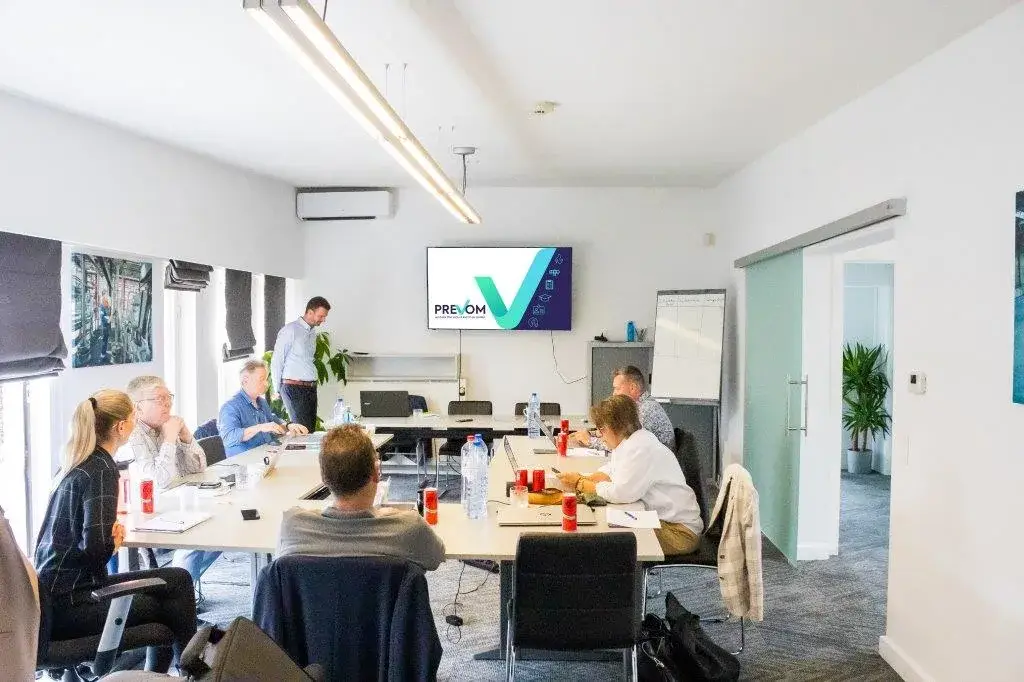
Inhoudsopgave
Wat is een toolboxmeeting?
Een toolboxmeeting is een kort moment waarop een specifiek veiligheidsconcept centraal staat binnen een team of afdeling. Tijdens deze bijeenkomst worden vaak ondersteunende visuele elementen zoals afbeeldingen, video’s of grafieken gebruikt, evenals concrete voorbeelden uit het eigen bedrijf of de sector. Wat een toolboxmeeting onderscheidt van conventionele preventiebijeenkomsten is de interactieve aanpak: de gebruikte voorbeelden en concepten vergroten het bewustzijn van medewerkers en brengen een productieve discussie op gang. Het doel is dat elke werknemer de meeting verlaat met een nieuw of hernieuwd inzicht in een specifiek veiligheidsaspect van hun dagelijkse werkzaamheden.
Hoe ziet een toolboxmeeting er uit?
De inhoud
Wat betreft de inhoud staat relevantie voorop: het doel is om een onderwerp te behandelen dat nauw aansluit bij de realiteit van de deelnemende medewerkers. Daarom is het niet ideaal om bijvoorbeeld een team vorkliftchauffeurs een toolboxmeeting te laten bijwonen over ergonomie op kantoor. Een meeting over het heffen van lasten met een vorklift op een hoog geplaatste locatie in een rek is natuurlijk veel boeiender. Beeldmateriaal, zoals foto’s van de werkvloer, maakt het behandelde onderwerp tastbaarder. Deze situaties zijn immers nog herkenbaarder voor de medewerkers dan generieke voorbeelden. Een PowerPointpresentatie kan tijdens de toolboxmeeting worden gebruikt, bij voorkeur eindigend met concrete tips en inzichten die medewerkers dagelijks kunnen toepassen voor een veiligere werkomgeving.
Hoe lang duurt een toolboxmeeting?
Een goede toolboxmeeting duurt ongeveer een kwartier of net iets langer.
Het is de bedoeling om op korte tijd heel wat nuttige inzichten en tips mee te geven: voorkom dat de meeting te lang doorgaat over de theorie, en focus op het overbrengen van waardevolle informatie.
Om het eenvoudiger te maken om de lengte te beperken, is het aan te raden om maximaal één of twee onderwerpen aan te snijden in een toolboxmeeting.
Wil je toch een uitgebreider onderwerp aanpakken? Tracht dit dan op te splitsen in meerdere toolboxmeetings: zo behoudt men de aandacht van de bijwoners en blijven de inzichten vaak beter ‘plakken’ dan bij een langere meeting die meerdere onderwerpen behandelt.
Frequentie
Voor VCA-gecertificeerde bedrijven is het organiseren van toolboxmeetings verplicht. De frequentie wordt bepaald door het VCA-niveau:
- VCA*: 4 keer per jaar
- VCA**: 10 keer per jaar
- VCA-P (petrochemie): 10 keer per jaar
Aanvullend op deze minimumvereisten is het aanbevolen om regelmatig toolboxmeetings te organiseren om de behandeling van onderwerpen ‘vers’ te houden en de link te leggen tussen voorgaande meetings.
Hou het simpel
Een effectieve toolboxmeeting is beknopt en to the point. Vermijd overmatig gebruik van technische termen en ingewikkelde voorbeelden. De inhoud moet concreet zijn, met de nadruk op de belangrijkste punten.
Zorg ervoor dat de inhoud concreet is; ga vooraf de meeting door en bekijk het vanuit het perspectief van de deelnemers. Wat zijn de essentiële punten die naar voren moeten komen? Het correct leggen van de nadruk draagt aanzienlijk bij aan de kwaliteit van de toolboxmeeting.
Voor wie is een toolboxmeeting?
De organisator
De organisator varieert per bedrijf, dit kan een interne of externe preventieadviseur, werfleider of productiechef zijn. Belangrijk is dat de organisator een goed inzicht heeft in de realiteit van het bedrijf.
De deelnemers
Alle werknemers moeten verplicht deelnemen aan een aantal toolboxmeetings volgens de VCA-norm. Kwaliteit en specificiteit zijn cruciaal bij het samenstellen van deelnemerslijsten. Een evenwichtige aanpak met zowel kwaliteit als kwantiteit is effectiever dan een beperkt aantal algemene meetings.
Gevaarlijke arbeid
Medewerkers die regelmatig gevaarlijke arbeid verrichten, krijgen vaak vaker toolboxmeetings. Ook medewerkers die minder in contact komen met gevaarlijke arbeidssituaties kunnen baat hebben bij periodieke voorlichting: een administratief medewerker heeft er bijvoorbeeld veel baat bij om toch basisinzichten te krijgen over de gevaren op de werkvloer.
Formeel of informeel? Combineer!
Een toolboxmeeting hoeft niet altijd in een formele vergaderruimte plaats te vinden. Het kan net zo effectief zijn op de werkvloer zelf. Een toolboxmeeting hoeft niet per se gepaard te gaan met een overvloed aan hulpmiddelen, PowerPoint en hand-outs. Het zoeken naar een balans tussen formele en informele benaderingen kan de impact vergroten.
Bijvoorbeeld, meer abstracte en complexe onderwerpen kunnen besproken worden op kantoor en begeleid worden met een PowerPoint, terwijl op de werkvloer meer concrete tips informeel kunnen worden gedeeld, zoals bijvoorbeeld over het dragen van veiligheidsgordels of het correct hanteren van apparatuur.
Wanneer een medewerker na 5 minuten weer plaatsneemt in zijn heftruck, kraan, graafmachine, enzovoort, kunnen zij deze praktische tips meteen toepassen in de dagelijkse realiteit.
Wat met onderaannemers?
VCA-gecertificeerde onderaannemers zijn verplicht om hun eigen toolboxmeetings te organiseren. Hoewel het niet verplicht is om toolboxmeetings voor onderaannemers te organiseren, kan dit wel zinvol zijn om een veilige samenwerking te waarborgen.
De succesformule
Een goede toolboxmeeting…
- Duurt kort (15-20 minuten)
- Wordt regelmatig georganiseerd
- Is to-the-point en relevant
- Behandelt 1 of 2 onderwerpen
- Stimuleert interactie
- Gebruikt alleen hulpmiddelen (slides, handouts, ...) als ze echt nuttig zijn
- Kan zowel op de werkvloer als in een vergaderruimte plaatsvinden
- Geeft de deelnemers niet het gevoel geviseerd of gestraft te worden
- Geeft de medewerkers concrete tips of actiepunten mee
Wanneer een toolboxmeeting aan al deze criteria voldoet, heeft deze ongetwijfeld een positieve invloed op de veiligheid op de werkvloer binnen uw bedrijf!
Op zoek naar duidelijkheid?
Is het erg dat een toolboxmeeting langer duurt? Moet ik bijhouden wie aanwezig was? Wat kost een toolboxmeeting? Wat als iemand niet komt opdagen?
Prevom heeft oplossingen op maat:
Wij informeren u graag over de mogelijkheden!